粉末高溫處理的工藝探究與實(shí)施
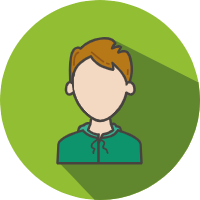
作者:翔宇粉末冶金制品
發(fā)布時(shí)間:2020-09-01 00:00:00
來源:本站 閱讀數(shù)量:1533次 點(diǎn)贊數(shù)量:1394次
渦輪轉(zhuǎn)子部件是航空發(fā)動(dòng)機(jī)重要的核心熱端部件之一,渦輪部件的材料必須具有高的屈服強(qiáng)度、拉伸強(qiáng)度和良好的熱穩(wěn)定性,能適應(yīng)高溫下可靠的工作要求。
隨著發(fā)動(dòng)機(jī)推重比的提高,粉末高溫合金材料越來越多地被采用,一方面給切削加工帶來很大的困難,無論是車削、銑削、拉削還是鉆孔,采用普通的硬質(zhì)合金刀具、高速鋼拉刀都不能滿足加工的需要;另一方面零件結(jié)構(gòu)上突出的特點(diǎn)是形狀復(fù)雜、壁薄、剛性差、圓弧轉(zhuǎn)接多,加工時(shí)極易產(chǎn)生變形,傳統(tǒng)的加工工藝都是靠成型刀加工型面來進(jìn)行加工,屬于面接觸加工,加工中切削力較大,增加了零件變形的產(chǎn)生。
因此必須研究新的加工工藝和應(yīng)用新型高硬度、高耐磨的刀具材料,引用高剛性、大功率的加工設(shè)備,優(yōu)化工藝路線,改進(jìn)傳統(tǒng)的加工方案,有效地控制并減少零件的加工變形,滿足高精度粉末冶金盤的加工需要。本課題以FGH96粉末渦輪盤為載體,重點(diǎn)從摸索粉末高溫合金材料的加工特性,優(yōu)化工藝方案、新型刀具材料切削試驗(yàn)及應(yīng)用,加工變形控制等方面進(jìn)行試驗(yàn)與研究。
1粉末渦輪盤結(jié)構(gòu)及加工工藝性分析1.1零件類型及結(jié)構(gòu)工藝性分析隨著發(fā)動(dòng)機(jī)推重比和渦輪前溫度的不斷提高,渦輪盤的應(yīng)力水平越來越高,傳統(tǒng)的變形高溫合金材料已經(jīng)不能滿足需要,而迫切要求使用具有高抗疲勞蠕變性能的粉末合金。粉末盤的出現(xiàn)解決了渦輪盤材料高合金化造成的凝固偏析和變形困難的問題,提高了力學(xué)性能,而且性能波動(dòng)小。在目前的渦輪盤制造技術(shù)中,粉末冶金已成為制造高性能渦輪盤最成熟、可靠的方法,國(guó)外已將粉末盤廣泛應(yīng)用于多種先進(jìn)發(fā)動(dòng)機(jī)的研制和生產(chǎn)中。
本課題所述粉末渦輪盤是大直徑、多型腔、結(jié)構(gòu)復(fù)雜的環(huán)形薄壁盤件,尺寸多、精度高,如所示。其帶有77個(gè)縱樹形榫槽,φB、φC、φD等多處直徑配合表面,尺寸精度要求高,輪盤輻板為不等厚結(jié)構(gòu),靠多處坐標(biāo)值控制輻板厚度。各型面轉(zhuǎn)接處為多圓弧與錐面轉(zhuǎn)接,要求轉(zhuǎn)接圓滑,且有輪廓度要求。在輪盤一側(cè)帶有伸臂安裝邊結(jié)構(gòu),其端面帶有弧齒。由于伸臂處安裝邊懸臂較長(zhǎng),直徑方向的壁厚僅為4mm,加工中極易產(chǎn)生變形,使得安裝邊處的內(nèi)腔型面加工難度增大,需要多把刀具轉(zhuǎn)接加工才能完成。輪盤上的端面弧齒是與壓氣機(jī)軸頸的連接部位,受力情況復(fù)雜,再加上材料硬度高、切削性能差等因素,零件的加工難度非常大。
1.2粉末高溫合金渦輪盤材料性能分析粉末盤采用FGH96材料制造,該材料具有較高的斷裂韌性和抗蠕變能力,其熱穩(wěn)定性及綜合性能良好。
粉末(鎳基)高溫合金晶粒細(xì)小,組織均勻,無宏觀偏析,合金化成度高,抗蠕變性能高、屈服強(qiáng)度高,疲勞性能好,是制造高推重比發(fā)動(dòng)機(jī)渦輪盤部件的最佳材料。目前在粉末高溫合金領(lǐng)域,美國(guó)和俄羅斯工藝各異,都居于世界領(lǐng)先地位。FGH96材料粉末盤的化學(xué)成分及力學(xué)性能見和。由材料的化學(xué)成分及性能指標(biāo)可看出該材料的切削加工性如下:(1)導(dǎo)熱性差,導(dǎo)熱系數(shù)僅為普通鋼的1/41/3,加工中傳熱困難,切削溫度很高,因此切削時(shí)容易產(chǎn)生粘刀現(xiàn)象。
(2)熱強(qiáng)性好,粉末高溫合金在較高的溫度下仍具有高的物理、機(jī)械性能,切削阻力比普通鋼高35倍。
(3)材料本身有大量的強(qiáng)化相,加工硬化嚴(yán)重,表面硬度比基體硬度高500,容易磨損刀具,降低刀具([url=http://www.chinaljrj.com/new_view.asp?id=365]數(shù)控刀具不斷創(chuàng)新促進(jìn)機(jī)床快速發(fā)展[/url])的耐用度和壽命。
由于粉末高溫合金具有這些性能特點(diǎn),所采用的刀具材料必須具有高強(qiáng)度、高紅硬性、良好的耐磨性好和韌性、高導(dǎo)熱性和強(qiáng)的抗粘接能力,并保持刀刃鋒利、排屑流暢。同時(shí)選用剛性好的工藝裝備(刀具、夾具和機(jī)床等)合理的切削用量(如較低的切削速度),進(jìn)給量適中,切削深度可較大,使刀尖在硬化層下工作,有利于提高刀具耐用度,加工時(shí)應(yīng)保持冷卻液充分的冷卻。
2切削加工試驗(yàn)粉末高溫合金在切削加工時(shí),由于上述材料的特點(diǎn),刀具磨損劇烈,刀具壽命明顯下降,在高切削溫度(750℃1℃)下,刀具產(chǎn)生嚴(yán)重的擴(kuò)散磨損和氧化磨損;加工硬化現(xiàn)象嚴(yán)重,已加工表面的硬化程度可達(dá)200以上。因此粉末高溫合金的切削加工性能低,切削加工困難大,通過試驗(yàn)來選擇最佳的刀具的材料和優(yōu)化切削參數(shù)是十分必要的。
為了更好地摸索粉末高溫合金的切削特性,用于切削試驗(yàn)的試驗(yàn)件和零件的材料完全一致,均為粉末高溫合金FGH96材料。
2.1粗車加工試驗(yàn)在進(jìn)行毛料的粗車加工時(shí),去除的余量較大,切削過程中沖擊性較大,由于此時(shí)對(duì)零件的表面粗糙度及尺寸精度要求不高,考慮到加工的經(jīng)濟(jì)性,所以在粗加工時(shí)首先在國(guó)產(chǎn)刀具材料中進(jìn)行選擇。
選用YD15、YG8和M42等不同材料的刀具分別進(jìn)行切削試驗(yàn),試驗(yàn)結(jié)果表明:YG8材料加工中刀具磨損嚴(yán)重,需頻繁換刀,甚至根本車不動(dòng)。
M42材料即使采用低的切削速度,也無法滿足加工需要,而且刀具磨損較快。YD15刀具晶粒細(xì)小,在車削過程中抗沖擊性較好,不易打刀,但切削速度較低,綜合考慮了多種因素,因此在粗加工時(shí)選用YD15材料刀具。
2.2半精車加工試驗(yàn)考慮到加工質(zhì)量和加工效率,在進(jìn)行半精加工時(shí)選用進(jìn)口刀具進(jìn)行了試驗(yàn)。先后選擇了陶瓷、立方氮化硼(CBN)、涂層硬質(zhì)合金及非涂層硬質(zhì)合金等材料的刀具進(jìn)行了試驗(yàn)。
通過對(duì)陶瓷刀具、硬質(zhì)合金刀具、涂層硬質(zhì)合金刀具分別對(duì)粉末高溫合金試件的切削對(duì)比試驗(yàn)可知:陶瓷刀具材料具有硬度高、耐磨性能好、耐熱性和化學(xué)穩(wěn)定性優(yōu)良、不易與金屬產(chǎn)生粘結(jié)特點(diǎn),在相同切削條件下,陶瓷刀具的耐用度高于硬質(zhì)合金刀具和涂層硬質(zhì)合金刀具,切削速度是硬質(zhì)合金刀具的45倍,更適合于粉末冶金零件的切削加工;在相同切削參數(shù)下,因?yàn)樘沾傻毒叩幕瘜W(xué)穩(wěn)定性較好且與試件的摩擦系數(shù)小,其加工表面粗糙度值小于涂層硬質(zhì)合金刀具。
(1)通過所選用陶瓷刀具和K類、S類硬質(zhì)合金刀具的切削對(duì)比試驗(yàn)可知:陶瓷刀具比這2種硬質(zhì)合金刀具更適合用于鎳基粉末高溫合金的半精車加工;(2)通過所選用陶瓷刀具和硬質(zhì)合金刀具切削力和表面粗糙度對(duì)比試驗(yàn)可知:在相同切削參數(shù)下,兩者的切削力相差不多,但陶瓷刀具的加工表面粗糙度值小于硬質(zhì)合金刀具。
(3)所選陶瓷刀具的磨損形態(tài)主要是前刀面的月牙洼磨損,主要破損形態(tài)是前刀面的剝落;前刀面主要磨損機(jī)理是擴(kuò)散磨損和磨粒磨損,后刀面主要磨損形態(tài)是磨粒磨損。
試驗(yàn)結(jié)果表明:在一定的范圍內(nèi),隨著進(jìn)給量的增大,加工表面的粗糙度值Ra明顯增大,而切削速度的變化對(duì)粗糙度影響不大;所以選用陶瓷刀具可進(jìn)行高速切削,且加工表面的粗糙度值明顯低于所選用硬質(zhì)合金刀具的加工表面粗糙度值。
2.3精車加工試驗(yàn)精車加工時(shí)重點(diǎn)考慮到零件的加工精度和表面粗糙度的要求,選用了CBN刀片和S05F復(fù)合涂層的硬質(zhì)合金刀具。
2.3.1CBN刀片切削試驗(yàn)切削用量:v=6065m/min,ap=0.20.3mm,f=0.1mm/r.
與硬質(zhì)合金相比,用CBN刀片車削粉末高溫合金時(shí)刀具磨損小,不僅加工質(zhì)量高,而且刀具壽命顯著提高,因而將CBN刀片用于精車,加工精度可以得到保證。由于粉末高溫合金材料中的Ni、Cr、Mo、Ti和Nb等元素在一定的切削溫度作用下與CBN刀片表面有較強(qiáng)的親合作用,因而發(fā)生較明顯的粘結(jié)。粘結(jié)會(huì)形成刀具表面的微粒脫落,造成粘結(jié)磨損。
當(dāng)切削溫度達(dá)到1000℃1刀具表面會(huì)產(chǎn)生氧化與放氮現(xiàn)象,過高的溫度還會(huì)產(chǎn)生CBN→HBN的轉(zhuǎn)化,使CBN刀刃失去切削能力。為此,在采用CBN刀具切削時(shí),必須注意選擇合適的切削用量和刀具幾何參數(shù),使切削溫度不致過高。
CBN刀具應(yīng)用的前提是:機(jī)床-工件-刀具系統(tǒng)要有足夠動(dòng)力和良好的剛性,而且工件以及機(jī)床要能承受高切削熱和大切削力帶來諸如變形等影響。因此必須控制切削力和切削振動(dòng)。
2.3.2S05F復(fù)合涂層材料硬質(zhì)合金刀具切削試驗(yàn)S05F涂層硬質(zhì)合金刀片,采用復(fù)合涂層,中間層涂層成分為:TiCN-Al2O3,表層涂層成分:MT-CVD化學(xué)涂層。
采用切削參數(shù):v=4560m/min,ap=0.20.3mm,f=0.1mm/r.S05F復(fù)合涂層材料適用于對(duì)硬質(zhì)合金刀具鋒利切削刃的涂覆,這一點(diǎn)對(duì)粉末高溫合金加工尤為重要。該涂層刀具切削性能好,耐用度高,適合于復(fù)雜型面、型腔的半精車和精車加工。切削試驗(yàn)證明,在很寬范圍運(yùn)用時(shí)這種組合涂層比其他任何一種單一涂層更有效,因此,應(yīng)用TiCN-Al2O3復(fù)合涂層材料的刀具,加工粉末高溫合金等難加工材料已成為應(yīng)用新涂層材料硬質(zhì)合金刀具的新亮點(diǎn)。
3粉末盤的加工工藝3.1工藝路線安排粉末盤毛坯采用模鍛件,熱處理狀態(tài):固溶 時(shí)效,HB≥388.根據(jù)以往加工盤類零件的經(jīng)驗(yàn)和對(duì)該盤件進(jìn)行工藝性分析,考慮到零件的結(jié)構(gòu)及材料的加工特點(diǎn)等因素,制定粉末盤主要加工工藝流程如所示。
3.2加工過程中注意的問題從中可以看出,粉末渦輪盤結(jié)構(gòu)復(fù)雜,型面點(diǎn)多,最小處壁厚只有4mm.在車削加工過程中,由于從毛坯到成品有較大的加工余量,因而會(huì)產(chǎn)生較大的切削力。加上材料本身的鍛造應(yīng)力的影響,零件加工中極易產(chǎn)生變形,從而造成零件尺寸難以保證,技術(shù)條件達(dá)不到設(shè)計(jì)要求。以精車加工為例,加工時(shí)首先將輪盤輻板型面的大部分余量去除,留0.10.2mm的余量時(shí),再加工端面A、直徑B等表面。加工中發(fā)現(xiàn)的問題集中體現(xiàn)在,將端面A、直徑φB基本加工到位,留有0.1mm左右的余量時(shí),再加工R3端面型槽,當(dāng)R3型槽加工合格后,卻發(fā)現(xiàn)尺寸(19.5±0.02)mm和直徑B尺寸φ298.6 0。
096mm均超出圖紙要求,說明其變形程度已經(jīng)超出了預(yù)留的加工余量,φ298.6mm尺寸縮小,19.5mm尺寸增大。同樣精車輪盤另一側(cè)時(shí),應(yīng)先將輻板處余量去除,在加工伸臂處安裝邊外圓φD和內(nèi)腔型面時(shí),為了保證外圓尺寸公差和壁厚要求,先車外圓,留0.2mm左右的余量,然后加工型腔處,最后再精車外圓,保證圖紙要求。
針對(duì)加工中暴露出的問題,及時(shí)調(diào)整了加工方案和優(yōu)化了加工順序和走刀軌跡,將預(yù)留的加工余量進(jìn)行了調(diào)整,并增加了精車修復(fù)工序,通過這些措施有效的減小了零件的加工變形,保證了尺寸精度和嚴(yán)格的技術(shù)要求。
3.3加工變形原因分析和控制措施3.3.1變形原因分析FGH96粉末高溫合金材料的加工難度大,以加工GH4169材料通用的YD15硬質(zhì)合金刀具為例進(jìn)行分析,加工FGH96材料其切削速度也只能達(dá)到加工GH4169材料的60,切削深度只能達(dá)到加工GH4169材料的50`,走刀量也不足GH4169材料的70,加工效率低,而且材料變形也很嚴(yán)重,大約為GH4169材料變形量的35倍。這給加工帶來了極大的困難,早日摸清粉末高溫合金材料的變形原因和變形規(guī)律,采取有效的控制措施,消除或降低變形所帶來尺寸超差,是亟待解決的問題。通過近些年對(duì)高溫合金、粉末高溫合金同等材料、不同的盤件以基本一致的工藝流程進(jìn)行加工中,摸索的變形規(guī)律,說明如下:(1)對(duì)于高溫合金、粉末高溫合金材料,加工中產(chǎn)生的變形不僅僅是機(jī)械加工中的切削應(yīng)力造成的,零件的毛坯鍛件在加工過程中內(nèi)應(yīng)力釋放后重新達(dá)到平衡狀態(tài)同樣會(huì)引起較大的變形。內(nèi)應(yīng)力的釋放過程,一是時(shí)間過程,零件加工的周期越長(zhǎng),內(nèi)應(yīng)力釋放的越充分,變形就越小,零件加工周期越短,內(nèi)應(yīng)力越不容易得到釋放,變形就越大。
(2)不同的材料就有不同的變形量。針對(duì)高溫合金和粉末高溫合金的機(jī)械加工,材料的去除量是造成零件變形的主要原因,切削余量大,切削應(yīng)力大,零件變形隨之增加。
(3)零件加工的工藝路線、加工順序和走刀軌跡、刀具材料的選擇、零件的裝夾方式等工藝方案是否先進(jìn)合理,直接影響到零件的加工變形。
3.3.2控制變形的措施(1)劃分加工階段,合理分配各工序的加工余量。
針對(duì)加工余量大、加工應(yīng)力集中引起變形的問題,應(yīng)優(yōu)化、細(xì)化加工工藝路線,合理分配各加工階段的加工余量,盡可能在粗加工時(shí)去除更多的余量,使零件盡早釋放應(yīng)力。
(2)優(yōu)化、固化切削參數(shù),在粗加工時(shí)控制切削深度不大于0.5mm,通過多次進(jìn)刀完成大余量的去除。這樣可以有效地減小加工應(yīng)力,精加工留有盡可能小的加工余量,保證最終加工后應(yīng)力較小。
(3)零件的型槽、型腔部位,對(duì)變形的影響很大,所以盡可能都要在精車加工前開槽。槽的深度盡量大,寬度可以稍窄些。精加工時(shí)轉(zhuǎn)接圓角部位的加工余量也要盡量小,這對(duì)減輕零件軸向尺寸的變形非常有利。
(4)盤類件的榫槽拉削加工后會(huì)產(chǎn)生較大的變形,一般精車加工后的所有徑向尺寸,經(jīng)拉榫槽后會(huì)普遍縮小,也會(huì)使零件各表面的形位公差值發(fā)生改變,因此應(yīng)摸索變形規(guī)律,采用尺寸補(bǔ)償?shù)姆椒ɑ蛟黾有迯?fù)加工工序消除變形的影響。
(5)增加消除應(yīng)力穩(wěn)定熱處理工序。
雖然采取了一系列減小加工應(yīng)力、控制加工變形的措施,但在粗車后和半精車后都要增加消除應(yīng)力穩(wěn)定熱處理工序,使加工中的應(yīng)力得到有效釋放,這樣可以減少精加工中的變形。
(6)噴丸前后的尺寸測(cè)量及修復(fù)加工。
噴丸過程中,由于丸粒是在一定的壓力下對(duì)零件表面的撞擊作用,在零件表面層產(chǎn)生壓應(yīng)力,同時(shí)噴丸強(qiáng)化過程中零件加工應(yīng)力也會(huì)得到一定釋放,所以不可避免地會(huì)使零件產(chǎn)生變形,造成零件尺寸發(fā)生變化。為了摸索出噴丸后尺寸變化規(guī)律,在噴丸前、后要對(duì)一些重要尺寸進(jìn)行測(cè)量,安排修復(fù)加工工序,對(duì)于難以修復(fù)的重要尺寸,則需要考慮在噴丸前預(yù)留變形量等尺寸補(bǔ)償辦法解決變形問題。
4粉末盤榫槽拉削4.1拉削技術(shù)要求粉末盤榫槽槽型及尺寸如所示:(1)滾棒距尺寸A1、A2偏差的差值不大于0.025mm;(2)任意兩榫槽之間F平面的高度差不大于0.025mm;(3)榫槽工作面在對(duì)稱平面方向上的相互最大允許錯(cuò)移量不大于0.02mm.
粉末盤兩側(cè)帶有安裝邊,尤其是一側(cè)伸臂處壁厚僅為4mm,使零件在夾具上定位裝夾困難,輪盤輪緣厚度較厚,拉削時(shí)拉削力大、剛性差,容易產(chǎn)生振動(dòng),使榫槽表面產(chǎn)生波紋,降低表面質(zhì)量,因此必須設(shè)計(jì)制造專用拉削夾具,增加其夾具底座的剛性和耐振性,保證夾具定位正確可靠。同時(shí)該零件榫槽深度尺寸比以往加工的盤類件榫槽要深得多,這樣必然使拉削力增大,因此設(shè)計(jì)成套拉刀時(shí)必須選擇合適的齒升量和拉削方案,通過試加工選擇確定最佳拉削速度。拉削中采用良好的冷卻潤(rùn)滑液進(jìn)行充分的冷卻。
4.2拉刀材料的選擇及拉刀方案設(shè)計(jì)由于此前沒有粉末高溫合金材料的拉削經(jīng)驗(yàn),通過查閱大量相關(guān)資料,采用進(jìn)口粉末高速鋼材料ASP2060制造拉刀,拉刀硬度HRC6668.
采用成套拉刀共14把,排成2排分2次拉削完成。第17把為開槽刀,第8把粗拉齒型,第911把為粗拉齒底槽刀,第12把粗拉齒頂圓弧刀,第13把精拉槽底圓弧,第14把為精拉齒形刀。其拉削示意圖即各把拉刀的拉削余量如所示。
4.3拉刀的工藝參數(shù)拉刀材料:ASP2060(粉末高速鋼材料)。拉刀前角:15°;后角:3°。齒升量:粗開槽刀為0.0450.06mm;粗拉齒型刀0.020.035mm;精拉槽底圓弧刀0.02mm;精拉齒形刀00.03mm.拉削方式:漸切式 全成型。
4.4使用設(shè)備采用進(jìn)口數(shù)控高速側(cè)拉床,主驅(qū)動(dòng)功率135kW,額定拉力25t,最大行程7.5mm.
4.5確定最佳拉削速度基于上述零件材料為FGH96的切削特點(diǎn),試驗(yàn)確定最佳拉削速度至關(guān)重要,考慮到現(xiàn)有機(jī)床行程7.5m,一套拉刀總長(zhǎng)10m,因此拉刀必須排2排才能完成加工。
根據(jù)以往加工GH4169材料渦輪盤的加工經(jīng)驗(yàn),同時(shí)考慮到粉末材料的難加工性,開始時(shí)采用了1.52m/min的拉削速度,但發(fā)現(xiàn)拉刀磨損嚴(yán)重,每拉削7個(gè)槽就需要卸下拉刀進(jìn)行重新刃磨,經(jīng)多次拉削試驗(yàn),最后將拉削速度調(diào)整為粗拉1m/min;精拉11.5m/min,取得了良好的拉削效果。
4.6拉削中出現(xiàn)的問題及改進(jìn)方案通過拉削過程中刀具的磨損情況和投影檢查結(jié)果發(fā)現(xiàn)影響拉削質(zhì)量和拉刀耐用度的主要因素有:(1)拉削速度。在數(shù)控高速側(cè)拉床上拉削,使用常規(guī)拉削GH4169材料的拉削速度2m/min,明顯發(fā)現(xiàn)拉刀磨損嚴(yán)重,榫槽表面粗糙度不好,經(jīng)多次試?yán)瓕⒗魉俣日{(diào)整為粗拉削1m/min,精拉削1.5m/min,取得了良好的拉削效果。
(2)投影檢查小試件發(fā)現(xiàn),榫槽輪廓轉(zhuǎn)接不圓滑,槽型局部有突起,經(jīng)研究確定了拉刀的修磨方案,對(duì)粗拉槽底拉刀進(jìn)行了結(jié)構(gòu)和拉削方式的改進(jìn),將原側(cè)面拉削改為頂齒拉削,同時(shí)將精拉齒型刀的齒距加大,避免了刀具的快速磨損,保證了榫槽輪廓形狀完全符合放大圖要求。
(3)在試?yán)鬟^程中,通過檢測(cè)發(fā)現(xiàn)輪盤輻板尺寸由于受到拉削力影響,輻板處向拉削方向產(chǎn)生了0.15mm左右的傾斜變形。通過對(duì)拉具結(jié)構(gòu)方案進(jìn)行改進(jìn),增加輔助支撐,有效地降低了拉削過程中的變形。
(4)粗拉齒底槽拉刀齒升量偏大,造成拉刀刀齒崩刃,經(jīng)重新進(jìn)行拉削試驗(yàn),改進(jìn)了拉削方式,降低齒升量,保證了拉削質(zhì)量。
(5)拉刀材料ASP2060含碳量高,拉削中發(fā)現(xiàn)材料脆性大,易產(chǎn)生崩齒現(xiàn)象,刀具材料改為T15粉末高速鋼后,拉刀壽命和耐用度提高。
5結(jié)束語先進(jìn)的制造技術(shù)是航空發(fā)動(dòng)機(jī)技術(shù)發(fā)展的基礎(chǔ),航空事業(yè)的發(fā)展依賴于材料、設(shè)計(jì)和加工技術(shù)的共同進(jìn)步,粉末盤的研制與應(yīng)用使我們的制造技術(shù)水平邁向了新的臺(tái)階。但就目前來說,我國(guó)在粉末盤制造技術(shù)領(lǐng)域與國(guó)外相比,存在較大的差距,特別是在機(jī)械加工方面,我們要快速開展切削技術(shù)研究工作,在消化吸收國(guó)際先進(jìn)制造技術(shù)的基礎(chǔ)上,結(jié)合新材料、新結(jié)構(gòu)、新工藝不斷應(yīng)用的實(shí)際需要,開展工藝制造技術(shù)的創(chuàng)新和探索,開展針對(duì)性的技術(shù)合作,大力提升制造技術(shù)水平。
感覺小編寫得不錯(cuò),給小編點(diǎn)個(gè)贊吧!
點(diǎn)贊最近更新
-
粉末冶金模具與產(chǎn)品的區(qū)別(粉末冶金模具多少錢一套)
時(shí)間:09-19 閱讀:243次
-
粉末冶金燒結(jié)的四個(gè)過程(粉末冶金燒結(jié)溫度如何確定)
時(shí)間:09-19 閱讀:356次
-
粉末冶金燒結(jié)的三個(gè)階段(粉末冶金燒結(jié)溫度如何確定)
時(shí)間:09-17 閱讀:497次
-
粉末冶金銅和鑄造銅的區(qū)別(粉末冶金和鑄造的優(yōu)缺點(diǎn))
時(shí)間:09-16 閱讀:364次
-
銅基粉末冶金如何加工的(銅基金屬粉體材料主要做什么)
時(shí)間:09-13 閱讀:194次
-
鐵基粉末冶金件的表面處理(鐵基粉末冶金燒結(jié)工藝)
時(shí)間:09-13 閱讀:245次
-
304粉末冶金的導(dǎo)熱系數(shù)(316l粉末冶金)
時(shí)間:09-13 閱讀:279次
-
粉末冶金的粉末金屬(粉末冶金主要成分)
時(shí)間:09-13 閱讀:235次
欄目
熱門閱讀
-
粉末冶金精度高嗎?精度可以達(dá)到多少?
時(shí)間:07-04 閱讀:10293次
-
粉末冶金強(qiáng)度多少?強(qiáng)度不足原因是什么?
時(shí)間:09-23 閱讀:7901次
-
粉末冶金與翻砂鑄造的優(yōu)劣對(duì)比
時(shí)間:08-25 閱讀:7305次
-
粉末冶金與壓鑄的的優(yōu)劣對(duì)比
時(shí)間:08-25 閱讀:6828次
-
粉末冶金與切削加工的優(yōu)劣對(duì)比
時(shí)間:11-16 閱讀:6630次
-
粉末冶金強(qiáng)度怎么?為什么還被廣泛應(yīng)用?
時(shí)間:10-29 閱讀:5871次
-
粉末冶金究竟是什么?其特點(diǎn)以及工藝流程怎么樣?立馬為你分享
時(shí)間:02-24 閱讀:5822次
-
粉末冶金工藝優(yōu)缺點(diǎn)分析,一文讀懂
時(shí)間:07-08 閱讀:5769次
-
干貨:粉末冶金制品的13種成型技術(shù)
時(shí)間:12-16 閱讀:4768次
-
粉末冶金與切削加工的優(yōu)劣對(duì)比
時(shí)間:11-16 閱讀:4040次